Qavi selected as one of the 4 finalist of the IISE M&D Division Best Student Paper competition
- dezhuotan
- May 21, 2022
- 1 min read
May 20, 2022.
This award recognizes excellence in the Institute of Industrial and Systems Engineers conference proceedings under the Manufacturing and Design Division.
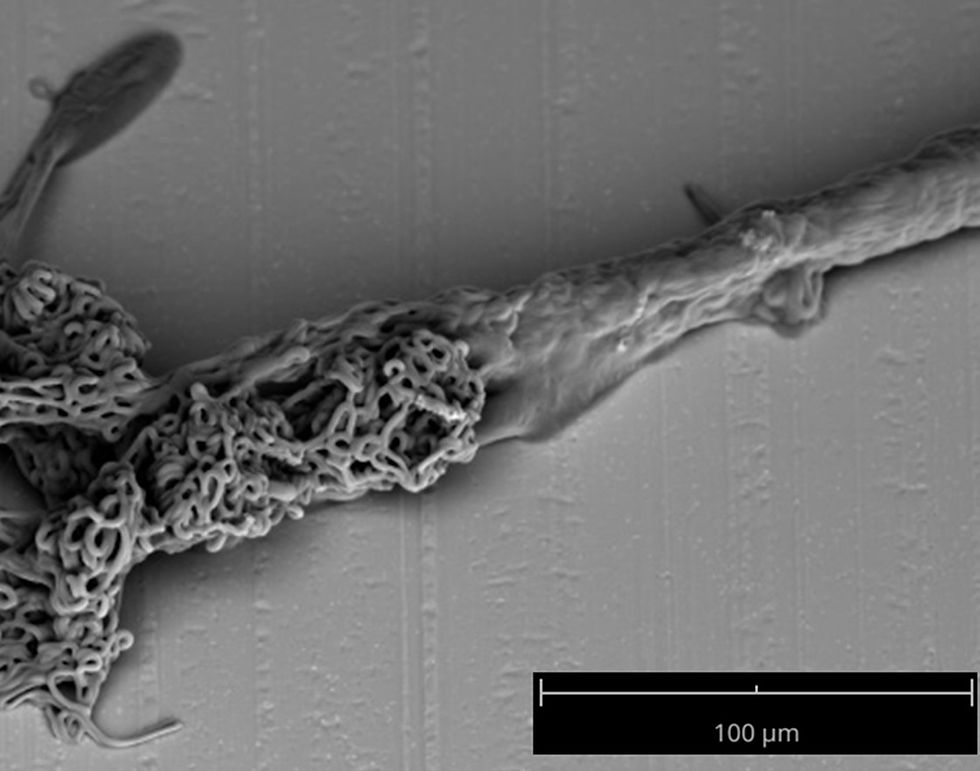
Near-field electrospinning (NFES) is a microfiber fabrication process in which the spinneret-to-collector distance is within 2 cm. We adopted the co-axial electrospinning to fabricate microfibers with polycaprolactone (PCL) sheath and polyethylene oxides (PEO) core. The NFES generated a continuous 3D structure composed of bundled microfibers with an average diameter of 1.4 μm. By using an inclining surface as the collector which gradually decreased the spinneret-to-collector distance from 2 to 1.5 cm, we obtained microfibers with a unique gradient structure. A bundle of microfibers merged into a larger single fiber with a diameter of 30 μm. This gradient structure captured the transition section of the electrospinning process in which a single jet spread into multiple whipping jets.
A slope collector resulted in a graduate change in fiber morphology - from a bundle of branched fibers to a continuous single fiber.
At a spinneret-collector distance of 2.0 cm, the NFES resulted in accumulated fibers within a band area which formed a bundle pile. The average height of the microfiber bundles was 64 µm. When the spinneret-to-collector distance reduced to 1.5 cm, the whipping disappeared. The electrospinning became electrohydrodynamic writing. This change led to the formation of a single fiber.
Biomimetic design for the arteriole-venule network
Understanding the mechanisms for such phenomenon will play a vital role in process development for microfibers with predefined patterns. Future studies on the formation of gradient fibrous structure by NFES will lay the foundation for fabricating biomimetic artificial vascular networks.
Comments